The general operation method of mixing in the open mill is to first add the raw rubber through the roll to the front roll, and leave a proper amount of accumulated glue on the top of the roll to cut off the excess rubber and feed according to the regulations. Add the compounding agent to the top of the stacking glue in sequence. When the raw rubber entrains the compounding agent through the roll distance, it is subjected to shear mixing, so that the compounding agent enters the inside of the rubber, which is called powder. When the powder is finished, it should be cut and tempered immediately. Finally, it must be thinned 3 to 5 times to ensure uniform mixing and dispersion, and then enlarge the roll to the next piece. The whole mixing process is divided into three stages: roll, powder and refining.
The rubber-coated roll is the premise of mixing in the open mill. Compounds that do not include rolls cannot be mixed with an open mill. The quality of the rubber roll is related to the characteristics of the raw rubber, the mixing temperature and the mechanical shear rate.
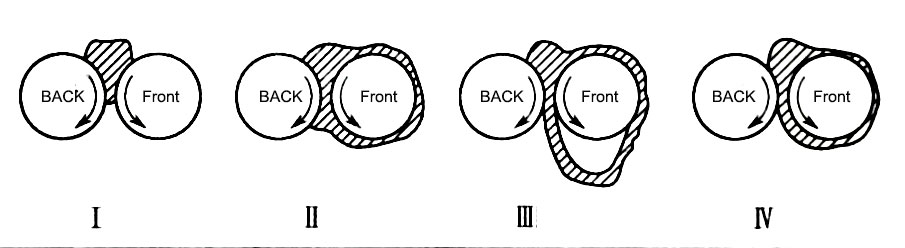
The figure above shows the state of the rolls on the rolls at different temperatures. It can be seen that in Zone I, the rubber is in the low temperature range and is in an elastic solid state. High hardness, high elasticity, and difficulty in entering the roll gap. If it is forced to pass, it will be destroyed and the roll cannot be wrapped and the mixture cannot be mixed. When the temperature rises to the range of Zone II, the rubber compound is a highly elastic solid with plastic flow and appropriate high elastic deformation. After the roller is placed, the elastic roller is used to tightly wrap the front roller, and the front roller does not break or roll, which is convenient. The mixing operation facilitates the mixing and dispersion of the compounding agent. When the temperature rises to the range of the region III, the rubber compound is still in a viscoelastic solid state, but its cohesive force and tensile strength are greatly lowered, and the fluidity is further increased. After the bag is removed or decomposed from the bag, the mixing operation cannot be performed; the temperature rises to a higher temperature range of the IV zone, and the rubber enters a viscous flow state. After passing through the roll gap, although it can be wrapped on the surface of the roll, the elasticity is reduced to a small extent, mainly due to plastic flow deformation, which causes the roll to adhere and is difficult to cut and refine. Therefore, during mixing in the mill, the temperature of the rolls should be maintained within the range of zone II to prevent entry into zones I and III.
Different raw rubbers have different temperature ranges in Zone II with good performance. Natural rubber and styrene-butadiene rubber have no obvious zone III at normal operating temperatures, only zone I and zone II, so the performance of the roll and the mixing performance are good. When the rubber is kneaded, the temperature of the roller should not exceed 50 ° C, otherwise the roll will occur. The temperature of the adjusting rolls should be kneaded in the temperature range of their respective zones according to the type of the compound.
The viscoelastic properties of the rubber are not only related to temperature, but also affected by the mechanical shear rate. Increasing the shear rate is equivalent to lowering the temperature. Therefore, when the rubber material is unrolled and the cooling is ineffective, the method of reducing the roll distance can restore the state of the wrapping roller. In addition, the molecular weight distribution of the rubber compound is wide, the temperature range of the 11-zone is good, the temperature range of the III zone is narrowed, and the mixing operation performance is good. The performance of the butadiene rubber and ethylene propylene rubber is poor, mainly due to the narrow molecular weight distribution and low cohesion of the rubber compound. After the carbon black is added to the rubber compound, the cohesive force and the tensile strength are improved, and the performance of the wrapping roller is improved.